We talk a lot of about spoilboards and sacrificial material, yet we still have customers encountering problems. Lately, we’ve had an increased number of customers call in about a lack of suction on their tables. There are a number of reasons why this could be happening. Perhaps the vacuum pump isn’t working correctly or the fittings aren’t secure. And yet the most common reason why a customer is experiencing a lack of suction? Their spoilboard.
We get that materials can be expensive and that picking up a piece of MDF at the lumber yard (or a piece that’s been lying around in your shop) is an inexpensive means of having a spoilboard. However, if you choose to use MDF you must TABLE MILL BOTH SIDES OF THE BOARD. This cannot be emphasized enough. MDF is created with a sealant, and this sealant prevents air from flowing properly through the board. If you do not route both sides of the board, air cannot pass through, and thus there will be a lack of suction on the piece you’d like to cut.
To create an MDF spoilboard, use a bit such as Onsrud’s 91-000 CT Spoilboard Cutter. If you’d like to use a material that doesn’t require the milling first, we recommend using LDF. LDF does not have the sealant that MDF has and its lower density means that air can more readily pass through, thus increasing your suction.
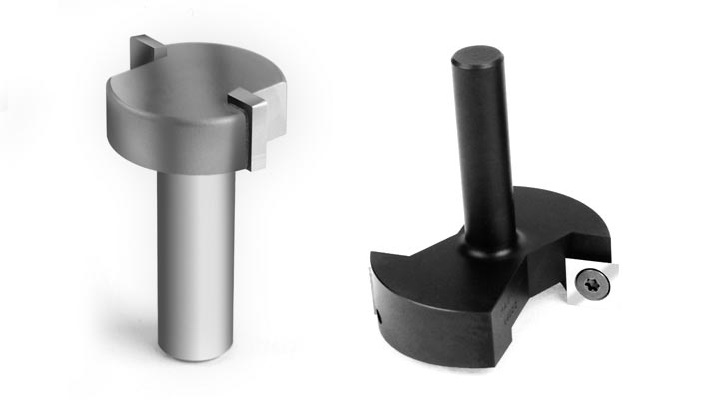
So before you’re frantically calling your CNC support technician think, could the suction have anything to do with my spoilboard? By ensuring you’re using the correct spoilboard, you could save time, money on service calls, and headaches.
Nice info!!!
ReplyDelete