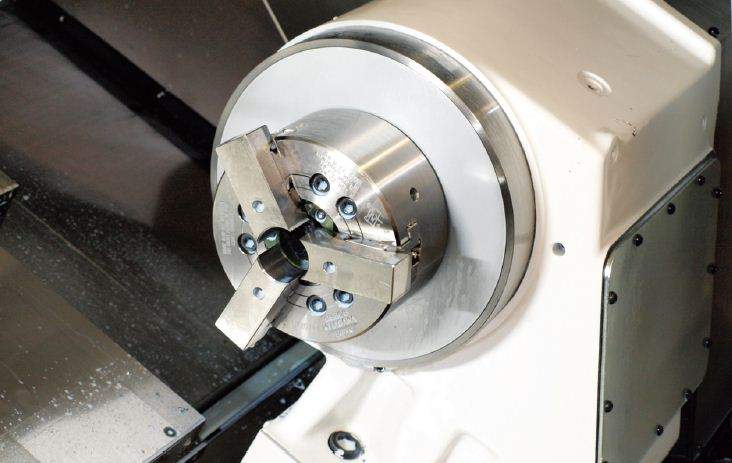
Here is an excellent article by Lindsay Luminoso from the Canadian MetalWorking Magazine, offering expert advice on how to extend spindle life.
“Out of sight, out of mind.” When it comes to spindle maintenance, this adage is more common than not. However, when manufacturers take this approach, they can often find themselves with spindle failures that can be both costly to repair and cause downtime and lags in production.
Overlooking this critical component can spell disaster and affect the bottom line. When you purchase a car, you don’t simply drive it without understanding the specific features and needs of the vehicle. Why would you do the same with your CNC machine and its spindle? Many operators will turn on the machine and run it without really understanding the capabilities and limitations of the spindle. Adding small checks and scheduling preventive maintenance can ensure long spindle life and increase productivity.
The spindle really is the heart of the machine and is designed with the application and user specifications in mind. Regardless of what type of machine you are running, the spindle allows the machine to function.
“Typically, when someone purchases say for example, a large milling centre, the spindle is so buried, but it’s the heart of the machine. You can build the most rigid machine in the world but you have to have a good spindle motor in there,” says Gary Quirion, corporate president of GMN USA.
Because the spindle is often hidden, it is sometimes forgotten about when the operator does machine checks and worse, can be unknowingly pushed beyond capabilities.
This is why it is so important to understand the features and specification of this critical component. The onus is on the owners and operators to keep their spindles in good working condition in order to maintain longevity. End-users need an education on the [specifications] of the machine. It’s not just plug-and-play for all its life,” explains Alexandre Maurais, president of MEC PRECISION. Maintaining proper machining practices and inspection of parts can mean the difference between a seized spindle and a spindle that lasts.
“The spindle life can be infinite, but only if it doesn’t crash,” says Gus Gustafson, service manager for Thomas Skinner & Son Ltd. Crashes occur when the operator pushes the machine to do something that it isn’t normally supposed to do; this can cause the spindle to stall and halt operations.
Unfortunately, this is a common occurrence on the shop floor. The spindle life really depends on how the operator treats it and how they run the machine. “The spindle life really varies. They can last 10-15 years under normal use. But if someone crashes it on a regular basis, it could last only a year or less,” continues Gustafson.
SIGNS OF A PROBLEM
There are some clear indicators that your machine’s spindle is in need of inspection or repair. Obviously, if the machine is no longer rotating, this could mean that the spindle has failed. The spindle itself is a highly sensitive component with many intricate parts. Rotating parts like the chucks, drawbars, quills, rotors, shafts, etc., should be handled with care to ensure that they are never hit and jarred, which can cause serious damage to the overall spindle abilities. Tolerances for the rotating parts are so tight that even the smallest push can cause failure. However, a spindle may not stall entirely, but there are some factors that can point to a future spindle failure. “Old school, if it’s noisy, or if you have part finish issues, or the spindle is running hot, those are good indicators,” says Quirion.
The experts agree that uncharacteristic noise is one of the key signs that there is a problem. Monitoring the spindle from the install and confirming that there are no abnormal or different noises is one way to keep the spindle spinning, say Maurais.
Cracking, humming or banging noises should be a clear indication for the operator to contact the maintenance department or spindle repair service to diagnose the problem.
A part finish can easily determine a problem with the spindle. Oftentimes, you can clearly see if a part has too much or too little material removed, or the workpiece finish is not correct. Slight variances in the tolerances can cause a part to fail inspection, and if several parts are constantly failing to pass quality inspection, then this can point to a spindle problem. Temperature can also point to a significant problem. When the spindle runs hot, abnormally hot, the operator should stop running the machine before further damage is done. The complex interior components of a spindle can vary significantly depending on the manufacturer or application. However, if the spindle is running above the average temperature, this can be an early indicator of a future problem. There are many ways to measure the temperature, including spindle temperature sensors that are often placed at the top and the bottom of the spindle providing live temperature feedback. Gustafson says that another option for measuring spindle temperature is a heat gun. The operator can measure the temperature themselves and compare against baselines set at that facility.
TIPS FOR OPERATORS
Enhancing spindle life is a fine balance between proper care and proper understanding of this high-precision component. The operator should know the ins and outs of the spindle as well as the machining applications. For example, machining titanium with low speeds and heavy loads can put a lot of stress on a spindle, while light grinding applications and lower speeds can extend spindle life. A typical spindle is designed with the application in mind but the external design is very similar. Internal components, like the angle of the bearings, the number of bearings, the preload, etc., that are developed for each machining application. This is why it is very important to read the manual and specifications for the spindle, especially because the spindle is tucked away in the machine and most operators generally don’t access it.
One of the most important tips Quirion has for extending spindle life is be safe. “I’ve seen many things over the years. I always say read the manual. You’d be surprised how many people call and ask a question, and I ask, ‘Did you see the manual on page such and such?’ and they don’t even have a manual,” he explains.
Speaking to the spindle manufacturer before operation can ensure proper use of the spindle. The manufacturer can provide guidelines that you might not even be aware of. One of the first things the operator can do is run a spindle warm-up program every shift, says Gustafson. As previously mentioned, increased temperature is an indicator of spindle issues. Measuring the temperature the spindle runs at after the warm up cycle is important for establishing a baseline.
Once the baseline is set, the operator can determine normal function of the spindle. If it is running hot, “then you know it is pointing towards a problem,” he explains.
Checking the cooling system to make sure it’s functional is also important. Whether the spindle is cooled through compressed air, liquid, or fan, it is important to make sure that the cooling mechanisms are running smoothly. In most cases, grinding and milling spindles will be liquid cooled. If you are able, it is always a good idea to observe the temperature of the bearings on the front housing. Maurais also points out that there are quite a few spindles that have a positive pressure around the nose. “There is air that is blown all the time so the coolant doesn’t go near the spindle or bearings. The air will stop blowing if the airline is dirty or cracked. [This] will contaminate the bearings quickly and the spindle won’t last long. We are telling customers to watch [out for this]. Make sure there is pressure of air around the bearings at the spindle nose,” he continues.
Experts agree that you must use caution when working with longer tools, as they may alter the rotor dynamics if not careful. For example, Quirion explains, “a spindle might run 60,000 rpm as advertised, but if a long grinding quill is put in it, the speed will be limited. And if the [operator] exceeds that, twofold, you will damage the spindle, and it’s a safety factor and someone can be injured.”
Ensuring that you are using the proper toolholder and appropriate concentricity of the taper to meet the manufacturer’s specifications is key. The toolholder’s tapered shank must fit perfectly in the spindle taper every time it is inserted. “There should be 100 per cent surface contact of the toolholder,” explains Maurais. This will keep the tool on the centre line of the spindle and allow for accurate and proper use.
Examining the contact surface of the taper can also be helpful. You want the contact to be at 100 per cent. Cleaning the toolholders and spindle can help maintain precision and prolong the life of the spindle and ancillary tools. Chips and coolant can often get caught between the tool and the taper interface, damaging both the spindle and the tool holder. Spindle cleaners are quality control products that can be used regularly to remove residual particles that can affect machining capabilities.
Another way to prevent a spindle failure is by making sure the load on the controller is normal. In many cases, the spindle load condition can be defined for particular tools, whereby the machine stops if it reaches this limit. However, verifying the proper settings ensures that an overload won’t occur.
As mentioned, machining something like titanium with heavy loads can put a lot of stress on a spindle. Make sure the spindle is qualified to perform such operations.

Proper care is really dictated by the type of spindle and application. For an oil-air system you have to make sure that all the settings are adjusted. Quirion explains, “You have to adjust the air and the oil flow rate. The drive unit has to be correct, the tool clamping for automatic tool change spindles have to be monitored, the tool retention should be checked and all the operating parameters with tool/without tool, those safeties should be checked.”
Day-to-day care can mean all the difference when it comes to spindle life. The operator should be aware of the spindle specifications and run the machine accordingly.
SCHEDULING PREVENTIVE MAINTENANCE
Aside from operator control, manufacturers can schedule Preventive Maintenance appointments with expert technicians who can come into the facility and run diagnostics on the spindles, providing data to allow for trending and extend general lifespan of the parts and spindle.
Experts agree that setting a Preventive Maintenance schedule at 3-, 6-, or 12-month intervals, can ensure spindle longevity.
There are many diagnostic tests that should be conducted on a regular basis. Having a thorough history or trending the machine and spindle function allows for manufacturers to plan ahead when it comes to a rebuild.
With Preventive Maintenance, “what we can do is tell you that ‘hey, your spindle probably has about six months left in it before it’s going to fail.’ And we can order the part and change it out for a customer before it even fails,” explains Gustafson. This allows for machine owners to anticipate future failures, which can be extremely costly, especially when it comes to unexpected breakdowns. Not all spindle manufacturers have all parts on the shelf and with new models, parts are not always readily available.
Preventive Maintenance tests can give a good indication when the spindle will need to be rebuilt, so parts can be pre-ordered, without expensive next-day delivery charges and production lags due to shipping times.
“The customers have a machine that cannot be down, cannot be in breakdown situations. The more we are able to prevent that, the more money everyone will make and the less emergency situations everyone will go through,” says Maurais.
There are 4-5 general Preventive Maintenance tests, including vibration test, checking the bearings, testing the pull force of the drawbar, and temperature checks.
Understanding how the spindle functions in the machine and the appropriate machining applications for the spindle can make all the difference when it comes to spindle longevity. Scheduling Preventive Maintenance appointments partnered with proper day-to-day operating techniques can ensure the spindle keeps on spinning for as long as you need.